Hello! I'm Wynand
I firmly believe that business survival in our highly competitive world is dependent upon reliably delivering high-quality products and services. I am dedicated to helping businesses (big and small) create business processes that enable them to meet business objectives and customers' expectations.

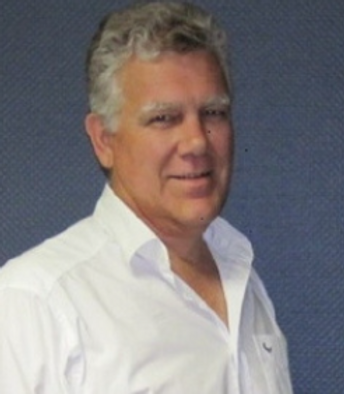
Business Process Consultant
+27 082 871 6708
Email:
Address:
5th Floor, Bloukrans Building
Lynnwood Road, Lynnwood Manour
Pretoria, 0081
SHEQ Years Experience
28 YEARS
Phone:
SKILLS

Business Process Mapping & Modelling; Redesign & Improvement
ISO Standards Facilitation & Implementation
Quality Assurance Systems - Advanced
SHEQ Management Systems
SHEQ System Management Support
SHEQ Training
EDUCATION
2019
USB (UNIVERSITY OF STELLENBOSCH):
LEADERSHIP DEVELOPMENT PROGRAM
2018
ISO 45001:2018
FACILITATION/ IMPLEMENTATION
2017
ISO 9001:2015
FACILITATION/ IMPLEMENTATION
2017
ISO 9001:2015
LEAD AUDITOR
2016
ISO 14001:2015
AWARENESS
2015
ISO 9001:2015
TRANSITIONS WORKSHOP
2014
BUSINESS PROCESS REDESIGN AND IMPROVEMENT
2013
BUSINESS PROCESS MAPPING AND MODELLING
2001
OSHSAS 18001:2007
INTERNAL AUDITOR TRAINING
2001
SABS IMPLEMENTATION AND EVALUATION OF QUALITY SYSTEMS:
ISO 9000: 2000
2000
UNIVERSITY OF PRETORIA:
MANAGEMENT DEVELOPMENT PROGRAM (MDP2/2000)
1999
CCA BEST PRACTICE PROGRAM FOR WORLD CLASS MANUFACTURING:
ACQUIRING OF KNOWLEDGE/SKILLS TO IMPLEMENT COMPETITIVE CAPABILITIES
1999
MRP II ACTIVE:
MATERIAL RESOURCE PLANNING II
1997
SOUTH AFRICAN QUALITY CENTRE:
INTERNAL QUALITY AUDITING
1995
SAMCOR:
8D – TOPS
1995
INDUSTRIAL TRAINING & QUALITY ASSURANCE (PTY) LTD:
QUALITY ADVANCED TECHNIQUES
1994
PRETORIA TECHNIKON:
VDA6 SYSTEM AUDIT
OSHSAS 18001:2007
INTERNAL AUDITOR TRAINING
1993
PRETORIA TECHNIKON:
NATIONAL HIGHER DIPLOMA QUALITY ASSURANCE
1989
AMSCOR:
QUALITY A AND B
1984
CAPE TECHNIKON:
NATIONAL DIPLOMA MECHANICAL ENGINEERING
KEY EXPERIENCE
2009-2022
BABCOCK ENGINEERING
MANAGEMENT SYSTEMS SPECIALIST
-
Ensuring the continuous development of a best-practice SHEQ management system consistent with integrated Babcock SHEQ Management system. (EBMS system)
-
Managing the consistent application and implementation of the Babcock SHEQ management system at Head Office and all Babcock sites, with specific focus on key activities including, but not limited to, resource management, process control, welding control, drawing control, documentation and data compilations and retention.
-
Responsible for measuring, through audits and process investigations, the effectiveness of the Babcock management systems and on-site processes (e.g., welding, data compilation etc), analyzing trends, developing/recommending corrective actions were appropriate.
-
To monitor the correction of any/all identified non-conformance's in accordance with the Babcock corrective and preventive action procedures.
-
Providing guidance and assistance where necessary in generating and maintaining process control documentation in accordance with the appropriate codes and contract specifications.
-
Assist whenever possible with the Quality Engineering function when required, e.g. project quality engineering.
-
Generation of monthly reports.
2002 – 2004
OPERATIONS MANAGER
BRILLIANT SECURITY SOLUTIONS
MANAGING OPERATIONAL AREAS: STORES, PURCHASING AND MANUFACTURING
-
Ensure timeous order and delivery of the correct goods.
-
Ensure meeting of required manufacturing schedules.
-
Culmination of technical data packs per product.
-
New product development/project planning.
-
Quality control.
-
Develop stores procedures and adherence there to.
-
Ensure that the minimum pre-determined stock levels are maintained.
MANAGE ADMINISTRATIVE SUPPORT FUNCTION TO OPERATIONS, TECHNICAL,MARKETING AND SALES.
-
Ensure the updating/maintenance of the sales/maintenance data base and the flow of information between sales, operations and technical departments.
AD-HOC FUNCTIONS
-
Manage human resources issues according to the basic conditions of employment act.
-
Vehicle management.
-
Ensure smooth functioning of admin functions.
1997 – 2002
QUALITY MANAGER
SMITH WHEELS (PTY) LTD
QUALITY SYSTEM
-
System.Responsible for implementing, controlling and maintaining an approved Quality Management
-
Internal / external auditing.
-
Customer liaison.
-
Identifying problem areas and initiating corrective and preventative action i.e., promoting the culture of "doing it right the first time”.
PLANNING
-
Planning and delegating tasks required to meet the quality standards / program while satisfying
-
Preparing and maintaining documentation to verify conformity with quality targets and standards e.g. quality costs, monthly reports, audit reports, management review.
​
TECHNOLOGY – PROCESS, PLANT & MACHINERY
Evaluating, periodically, the adequacy of establishing technology with reference to projected production volumes and prescribed quality standards.
​
BUDGET CONTROL
Submitting proposals, annually, in respect of budgets. Evaluating all items of expenditure regularly
​
HUMAN RESOURCES
-
Reviewing the make up and size of departmental complements for the purpose of projecte production volumes, maintaining projected quality standards and targets and complying with labour budgets.
-
Ensuring that vacancies in all sections are promptly filled with competent people.
-
Monitoring and identifying employees for appropriate training and development programs.
-
Monitoring relationships, within working groups, between foremen, supervisors and their subordinates, with shop stewards, labour turnover and absenteeism statistics.
PACKAGING AREA
Ensure that wheels are packed according to production orders
CCA –BEST PRACTICE PROGRAM FOR WORLD CLASS MANUFACTURING
Co-ordinating all activities to train and implement best practice within the company.
EXPERTISE
Quality Management Systems
Business Process Development
Facilitation for ISO Certification
I'm an expert facilitator, developer, and implementor of effective ISO 9001 management systems.
My years of experience in the SHEQ field also enable me to make a valuable contribution to the training of the next generation of QMS practitioners.
I have extensive experience in developing core, management, and support business processes. The companies I served daily rely upon my processes to deliver high-quality products and services. I'm proud and delighted to have been able to contribute to their success.
I've worked on countless business process development projects for small, medium, and large companies; including facilitation and preparation for ISO 9001 certification. My experience is particularly wide-ranging in the manufacturing environment.